Breathe a little easier with a new approach in chemical recycling
- ACS BCP
- Sep 25, 2021
- 2 min read
For the few plastics that get recycled globally in the waste management industry, the dominant approach adopted has been mechanical recycling. However, mechanical recycling merely washes the plastics and melts them down again. It also struggles with issues of contamination, is not cost-effective, and is difficult to carry out in many cases. Chemical recycling aims to solve this. It works by turning plastic waste back into base chemicals. For example, pyrolysis can break down waste HDPE into liquid hydrocarbon products. It has shown great potential in 2020 and is predicted to have a significant growth in profit from 2016 to 2020. This can improve recycling rates hugely and offer a more sustainable way to reuse plastic waste by avoiding landfills and incineration.
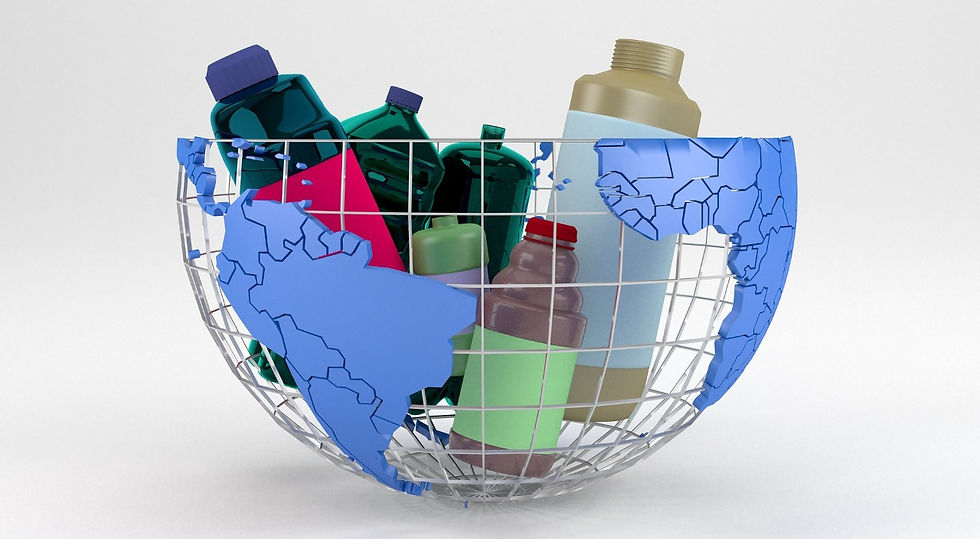
A recent study conducted at Cornell University by Xiang Zhao and Fengqi You proposes a framework for chemical recycling. The paper titled Consequential Life Cycle Assessment and Optimization of High-Density Polyethylene Plastic Waste Chemical Recycling discusses this framework, considering a series of factors for making it sustainable and cost-effective.
The first factor is superstructure optimization, which involves the creation of an optimal process. The second is the consequential life cycle assessment approach, which determines the effects of production and the end product on the environment. The third and fourth factors are market equilibrium models and techno-economic analysis, which consider market assessments and the economic viability of the waste HDPE recycling pathway.
The methodology itself consists of seven processing sections, the first being fast pyrolysis of shredded waste HDPE particles using either SiO2 or HZSM-5.
The next sections involve light and heavy downstream product separation, which result in the manufacturing of 1-butene, butane, isobutene, and light naphtha.
The process then moves on to the sections of aromatic extraction and hydroprocessing. The end result of these is the production of liquid hydrocarbon products such as gasoline, diesel, and aromatic mixture.
The final sections are the production of hydrogen and electricity generation at the site itself. The aim of these is to reduce the impact on the environment resulting from offsite production.
This approach has shown great potential and more efficiency compared to the analytical tools used in the past.
The authors then describe the market dynamics of the products and by-products. One such observation is that producing butene onsite instead of sourcing it reduces photochemical air pollution resulting from recycling plants almost by 20 percent.
The increased economic benefit coupled with decreased environmental impact makes Consequential Life Cycle Optimization a technology to watch out for in the field of plastics and chemical recycling for experts and policy makers alike.
Reference:
Xiang Zhao et al, Consequential Life Cycle Assessment and Optimization of High-Density Polyethylene Plastic Waste Chemical Recycling, ACS Sustainable Chemistry & Engineering (2021).
Blog by Bishakha Choudhary
Oh wow ! This is going to bring big changes in climate protection policies and create a value in previously unrecyclable plastic waste. With it expanding to an industrial scale in the near future, makes me think that maybe we can expect a scenario in which like 50% of plastics worldwide could be reused or recycled around 2030 or so. This is a great find! I would love to see more interesting ideas coming from the blogger!