From Landfill to Luxe: Regenerated Fashion Fabrics
- ACS BCP
- Jan 12
- 4 min read
Introduction: Regenerated fibers [RFs] are revolutionizing the textile industry by blending sustainability with innovation. These fibers, crafted from agricultural waste and other renewable sources, are paving the way for eco-friendly alternatives to traditional textiles, which are often resource-intensive and environmentally damaging.
With the fashion industry under increasing scrutiny for its environmental footprint, regenerated fibers offer a promising solution to combat waste and reduce reliance on non-renewable materials.
What Are Regenerated Fibers?
Regenerated fibers are man-made fibers produced by converting natural materials, such as proteins or cellulose, into new textile materials. They bridge the gap between natural and synthetic fibers by combining the benefits of both.
Cellulose-Based Fibers: Made from agricultural waste like plant cellulose, transformed into materials like rayon and viscose.
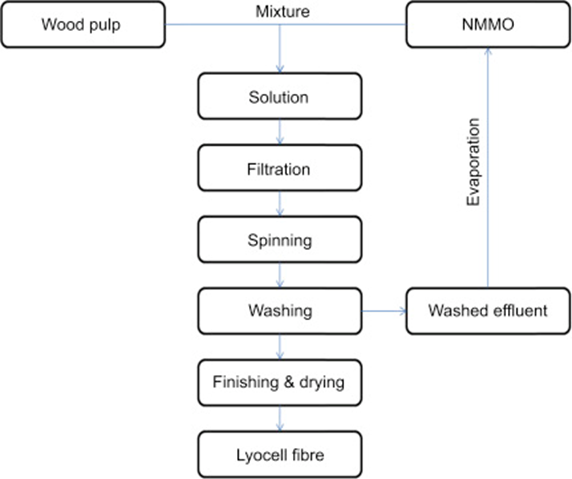
The Lyocell manufacturing process begins with industrial dissolving pulp containing 96% cellulose, which is dispersed in a concentrated aqueous solution of N-methylmorpholine N-oxide (NMMO) and water. The mixture typically consists of 67% NMMO, 20% water, and 13% cellulose. Under shear forces and controlled heating at 120°C, the water gradually evaporates, leading to the dissolution of cellulose and the formation of a highly viscous solution.
The cellulose solution is then filtered to remove impurities and extruded through fine jets into a water bath. During this process, the solvent is washed out, allowing the cellulose to solidify into fine filaments. These filaments are collected as tow and subsequently processed into staple fibers. After fiber formation, water is evaporated from the system, and the concentrated NMMO is recycled back into the production cycle, further enhancing the environmental benefits of Lyocell manufacturing.
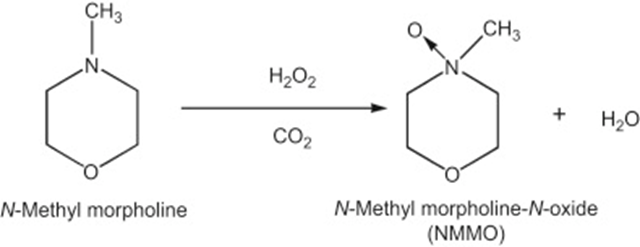
Lyocell serves as a sustainable alternative to viscose due to its environmentally friendly manufacturing process. Unlike viscose, which relies on chemical reactions involving NaOH and CS₂ (resulting in harmful by-products), It employs physical dissolution using non-toxic NMMO without chemical reactions. Lyocell fibers are spun through dry-jet wet spinning, achieving highly crystalline and durable structures, whereas viscose fibers are relatively amorphous with lower tenacity. Moreover, by recycling over 99% of the solvent used, there is significant reduction in environmental impact, while viscose production loses 25–30% of CS₂, contributing to environmental harm. With no harmful by-products and reduced water demand, Lyocell offers a greener and more efficient alternative for textile manufacturing. Another method by which RFs are produced is using the leftover residue from citrus peels after extraction of the juice. The wet citrus residual, is processed with a patented chemical method to be able to extract the cellulose that will form the final yarn and textiles are made from them.
Regenerated Protein Fibers [RPFs]: Derived from casein, soy, and gelatin, mimicking silk and wool.
Building on the sustainable advancements of cellulose-based fibers like Lyocell, protein-based regenerated fibers offer another innovative approach to eco-friendly textiles, utilizing natural protein sources to mimic
the luxurious qualities of silk and wool.
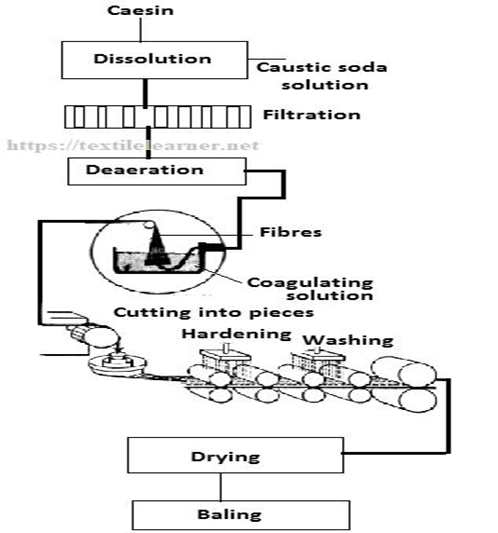
To overcome the toxicity of formaldehyde used in the coagulation bath another method utilizing cross-linkers is used. Casein is dissolved in an alkaline solution to create a pliable form suitable for fiber formation and cross-linking agents, such as glutaraldehyde or isocyanates, are then added to the casein solution to form covalent bonds between casein molecules. This cross-linking reaction strengthens the fibers by creating a more stable molecular structure. For instance, glutaraldehyde reacts with the amine or carboxyl groups of casein to form a network of cross-linked molecules. After the cross-linking reaction, the casein solution is extruded through a spinneret into a coagulation bath, usually containing an acid or salt solution, where the fibers precipitate. The fibers are then stretched to enhance alignment and strength, followed by washing to remove any residual chemicals. Finally, the fibers are dried to solidify their structure. This process results in strong, biodegradable casein fibers with applications in textiles and packaging. Additionally, the role of casein fibers in wound healing is actively being explored.

Economical Implications:
The economic implications of regenerated fibers (RFs) are multifaceted, influencing both production costs and market dynamics. By utilizing renewable resources and agricultural waste, RFs lower raw material expenses while promoting waste valorisation. Their energy-efficient and resource-recycling production processes, further reduce operational costs, making them an economically viable alternative to synthetic fibers. As consumer demand for sustainable products grows, RFs attract premium pricing, boosting profitability for manufacturers. However, initial setup costs and scaling challenges for innovative processes may pose short-term financial barriers for some manufacturers. Future Scope:
The future of regenerated fibers is promising, with continued research aiming to enhance their sustainability and functionality. In the textile industry, advancements in the production of protein-based fibers like casein and cellulose-based fibers like Lyocell could lead to more eco-friendly, high-performance materials. As consumer demand for sustainable products grows, RFs will likely play a significant role in reducing the environmental impact of textiles. Additionally, the exploration of RFs in medical applications, such as wound healing and biodegradable implants, opens new avenues for innovation. Advancements in cost-efficient production technologies can make regenerated fibers more economically viable, encouraging wider adoption across the fashion industry.
Conclusion:
Regenerated fibers represent a crucial step toward a more sustainable and environmentally conscious textile industry. By leveraging natural resources and innovative manufacturing processes, these fibers offer eco-friendly alternatives to traditional textiles, while also opening doors to new applications in medical and packaging fields. As technology and research progress, regenerated fibers will become increasingly central to both the fashion and biomedical industries. Embracing regenerated fibers not only addresses environmental concerns but also presents an opportunity to create sustainable economic models for the future of textiles.
References:
6. https://www.researchgate.net/publication/24420809_Effect_of_Cross-Linking_on_Microstructure_and_Physical_Performance_of_Casein_Protein 7. https://doi.org/10.20546/ijcmas.2018.704.140
-By Heta Hasurkar
Comments